In the UK, the Energy Savings Opportunity Scheme (ESOS) mandates comprehensive energy audits for large enterprises. This initiative, implemented by the government, ensures organisations engage in energy reduction and decarbonisation efforts. While ESOS assessments are a step towards energy efficiency, they often overlook high-energy-intensive processes within factories, leaving a significant gap in potential energy savings.
Understanding ESOS
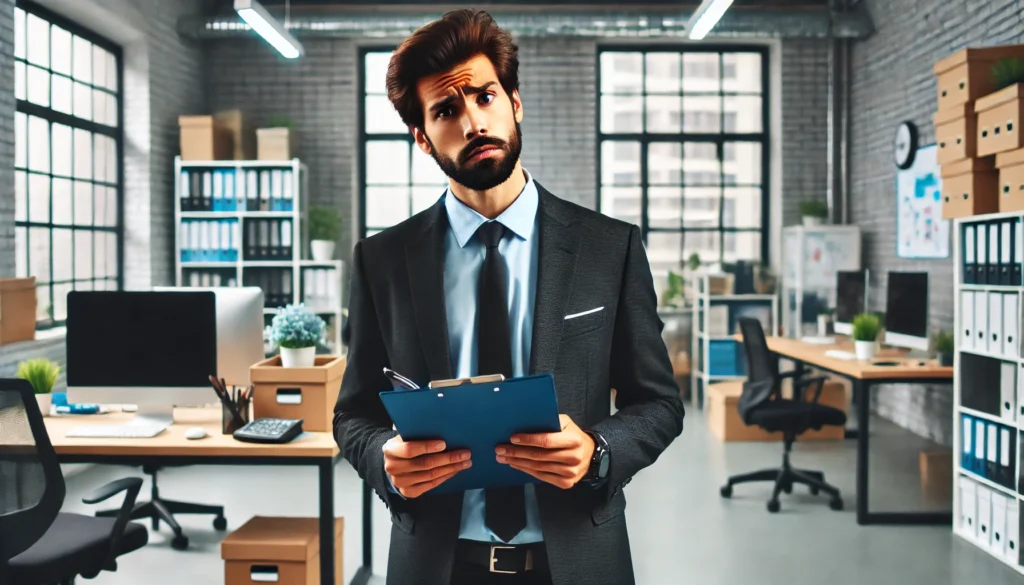
The Energy Savings Opportunity Scheme (ESOS) is a mandatory energy assessment and energy-saving identification scheme for large organisations in the UK. Introduced in response to the EU Energy Efficiency Directive, ESOS aims to reduce energy consumption and improve energy efficiency across large enterprises. ESOS operates in compliance periods or phases, each lasting four years. Currently, we are in Phase 3, which requires organisations to complete their energy audits and report compliance by 5 June 2024 (previously 5 December 2023).
What Qualifies as a Large Organisation?
To qualify for ESOS, an organisation must either employ 250 or more people or have an annual turnover in excess of €50 million (approximately £44 million) and an annual balance sheet total in excess of €43 million (approximately £38 million). Organisations that meet these criteria must conduct ESOS assessments every four years to evaluate their energy usage across buildings, processes, and transportation.
Compliance and Penalties
Non-compliance with ESOS can lead to significant penalties. The Environment Agency has the authority to impose fines, and non-compliant companies may have their names published as part of a “name and shame” process. This underscores the importance of meeting the compliance deadlines and following the guidelines meticulously.
The Current State of ESOS Assessments
Typical ESOS assessments focus on obvious areas of energy consumption such as electrical requirements, HVAC systems, and lighting. These elements are important but do not cover the entirety of a factory’s energy usage. High-energy processes, which can account for a substantial portion of a factory’s total energy consumption, often receive cursory attention. This oversight results in missed opportunities for significant energy savings and efficiency improvements.
Areas Often Overlooked
High-energy processes like smelting, extrusion, or chemical processing are frequently under-assessed. These operations consume vast amounts of energy, and without thorough audits, the potential for substantial energy savings remains untapped. Standard ESOS assessments may prioritize easier, more visible improvements, such as upgrading lighting or HVAC systems, but these measures alone do not address the full scope of energy use.
Does Your ESOS Assessment Really Provide a Path to Net Zero?
A critical question for businesses is whether their current ESOS assessment truly paves the way to achieving net zero emissions. While these assessments help identify areas for improvement, the limited focus on high-energy processes means many companies are not fully addressing their carbon footprint. Achieving net zero and significant CO2 emission reductions require a comprehensive approach that includes all major energy consumers within the facility.
Comprehensive Energy Audits
A comprehensive energy audit should include a detailed analysis of all energy-consuming processes within a facility. This includes an in-depth look at high-energy-intensive processes, which are often the largest contributors to a factory’s overall energy use. Without this, businesses miss out on opportunities for significant energy and cost savings, as well as progress toward their net zero goals.
Real-World Implications
Consider a large manufacturing plant with multiple high-energy processes such as smelting, extrusion, or chemical processing. These operations consume vast amounts of energy but might only receive a brief review during a standard ESOS assessment. The primary focus might instead be on optimising the HVAC system or switching to LED lighting. While these measures are beneficial, they do not address the core of the factory’s energy use, leaving the potential for greater savings untapped.
Case Studies and Examples
Real-world examples highlight the gap in typical ESOS assessments. For instance, a large plant involved in chemical processing might find that its primary energy consumption comes from the high-energy processes involved in production, yet these areas are only superficially audited. By focusing only on secondary energy uses like lighting and heating, the plant misses significant opportunities for energy reduction and cost savings.
The Need for a Comprehensive Approach
To maximise energy efficiency, it is essential to conduct thorough audits that delve into high-energy-intensive processes. This is where Enertherm Engineering can make a significant difference. Our team specialises in detailed energy audits and pinch analysis, a methodology that identifies the most efficient ways to reduce energy consumption by analysing thermodynamic processes within the factory.
The Role of Pinch Analysis
Pinch analysis is a powerful tool that goes beyond surface-level energy audits. It involves a detailed examination of energy flows within a process, identifying where energy can be recovered, reused, or reduced. By applying pinch analysis, we can uncover substantial savings often missed in standard ESOS assessments. This method not only reduces energy costs but also enhances overall process efficiency and sustainability.
Conclusion
Factories and large enterprises should not settle for the basics when it comes to energy audits. The stakes are too high, both in terms of potential savings and environmental impact. We urge businesses to look beyond standard ESOS assessments and invest in comprehensive energy audits that address all areas of energy consumption, especially high-energy-intensive processes.
Partnering with Enertherm Engineering
At Enertherm Engineering, we are committed to helping businesses achieve their energy efficiency goals. Our expertise in conducting detailed audits and pinch analysis ensures no stone is left unturned in the quest for energy savings. Contact us today to learn how we can help you capture the full potential of your factory’s energy use and drive meaningful improvements.
Implementing Best Practices
We recommend integrating comprehensive energy audits into your regular maintenance schedule. This ensures ongoing identification of energy-saving opportunities and keeps your facility operating at peak efficiency. Additionally, involving cross-functional teams in the auditing process can provide diverse insights and foster a culture of energy awareness within your organisation.
By addressing the high-energy users within your facility, we can make a substantial impact on your energy consumption and cost savings. Let’s work together to create a more efficient and sustainable future.