The method by which we dry our food and other industrial products has a significant impact on both the final quality of the product and our health. While direct fire drying has been a long-standing practice across many industries from agriculture to whisky production, growing concerns about its potential health risks, particularly the formation of carcinogens, are leading many to explore the advantages of indirect fire drying methods. This article looks into the differences between these two drying methods, highlighting the health and safety benefits of indirect drying.
Understanding Direct Fire Drying
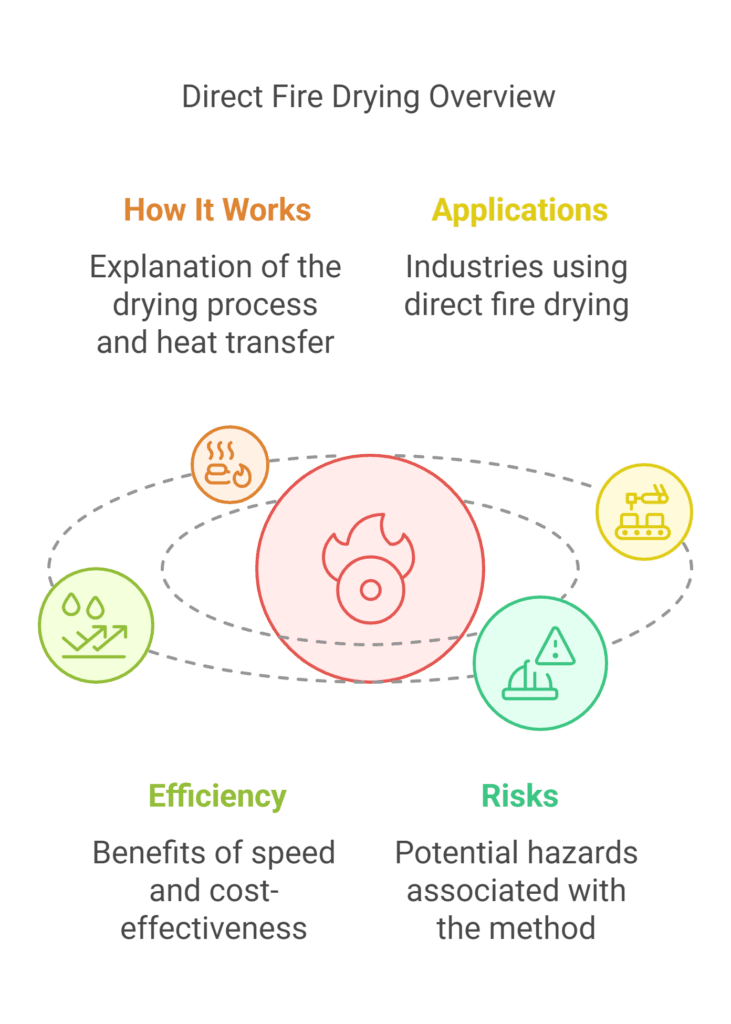
Direct fire drying involves exposing the material being dried directly to the heat source, often through combustion gases. This method is commonly used in rotary dryers, where the material passes through a rotating drum and comes into direct contact with hot air or gas. While this approach is efficient and cost-effective, it carries inherent risks.
How Direct Fire Drying Works
In a direct-fired rotary dryer, the material to be dried is fed into a rotating drum, where it is lifted by internal flights, causing it to cascade through a stream of hot gases. These gases may be the products of combustion, heated air, or other specialty gases. The direct contact between the material and the hot gas facilitates rapid drying due to effective heat transfer. This method is popular for its efficiency and speed.
Direct Fire Drying in Various Industries
- Agriculture: Direct fire drying is often used for grains and other crops. In this method, the hot gases directly contact the agricultural products, quickly removing moisture.
- Whisky Production: Some distilleries use direct fire to heat the stills. This traditional method involves heating the base of the pot with a flame from burning coal or gas.
- Food Processing: Direct-fired heating systems have been used in spray drying processes for products such as milk powder and soup mixes.
The Health Risks of Direct Fire Drying
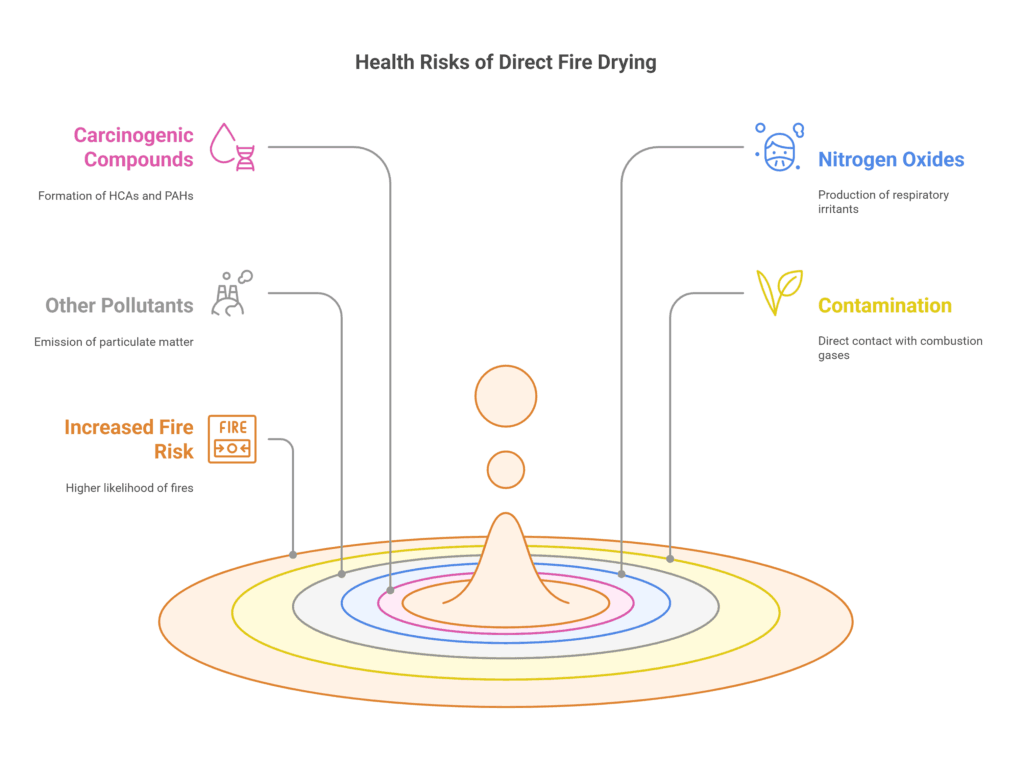
The most pressing concern with direct fire drying is the potential for the formation of harmful byproducts, especially carcinogenic compounds. These include:
Heterocyclic Amines (HCAs) and Polycyclic Aromatic Hydrocarbons (PAHs)
When meat or other protein-rich foods are exposed to high temperatures from direct flames or hot surfaces, HCAs and PAHs are formed. These chemical compounds are known to be mutagenic, meaning they can cause changes in DNA that elevate the risk of cancer. The combustion products adhere to the material being dried, introducing these harmful compounds to the final product.
Nitrogen Oxides (NOx)
Direct fire systems can produce nitrogen oxides as a byproduct of the combustion process. These gases are respiratory irritants and can pose risks, especially in poorly ventilated areas. High flame temperatures, typically above 1500°C, significantly increase NOx production.
Other Pollutants
Direct-fired systems may also emit particulate matter and other harmful gases, posing additional health risks. These emissions can contribute to respiratory problems and other health issues when inhaled.
Contamination
In food processing, direct contact with combustion gases can lead to contamination of the final product with undesirable byproducts of the combustion process.
Increased Risk of Fires
Direct-fired systems, particularly in grain drying, carry an increased risk of fire. While fires can occur in both direct and indirect systems, the direct contact with combustion gases elevates this risk.
Indirect Fire Drying: A Healthier and Safer Alternative

Indirect fire drying employs a different approach by using a heat exchanger to transfer heat to the material without direct contact with combustion gases. The heat is transferred through an intermediate medium, such as hot fluid or steam, to the vessel containing the product. This method offers several health, safety, and quality advantages over direct fire drying. For efficient and contamination-free heating solutions, consider our indirect air process heaters, which provide safe heat transfer without direct combustion contact.
How Indirect Fire Drying Works
In an indirect system, heat is applied to the shell of the drying drum or a series of tubes located circumferentially to the cylinder. This is often achieved through steam jacketing, oil heating, or furnace encasement. The material is heated via conduction and radiation, not by direct contact with the combustion gases. This means the drying environment can be more tightly controlled, and the material is not exposed to harmful combustion products.
Advantages of Indirect Fire Drying
Reduced Carcinogen Formation
By avoiding direct contact with combustion gases, indirect drying significantly minimizes the formation of HCAs, PAHs, and other harmful compounds. This results in a safer and healthier final product.
No Exposure to Combustion Byproducts
Indirect systems ensure the material being dried is not exposed to combustion gases and their potentially harmful emissions, like NOx and particulate matter. The furnace exhaust is kept separate from the process gas, reducing the need for exit gas treatment.
Enhanced Control
Indirect drying allows for more precise temperature control and a more uniform drying process. This is especially important when processing materials that are heat-sensitive or require specific atmospheric conditions. It also reduces the risk of uneven drying or overheating.
Lower Risk of Fire
Indirect drying, particularly when employing steam or hot oil as the heating medium, presents a lower risk of fire compared to direct fire systems. This is because the heat source is contained, and there is no direct exposure to open flames.
Preservation of Nutritional Properties
Indirect drying can better preserve the nutritional properties of food products because they are not exposed to the extreme heat and combustion byproducts associated with direct fire systems. This means less degradation of vitamins, antioxidants, and other beneficial compounds.
Suitable for Fine and Dusty Materials
Indirect dryers are ideal for processing dusty or fine materials, which might become entrained in the process gas of direct dryers. They also work well for materials that cannot be exposed to oxygen or combustion gases during processing.
Reduced Environmental Impact
By containing combustion gases and not exposing them directly to the drying material, indirect systems often have a reduced environmental impact. They also allow for better control and reduction of harmful gas emissions into the atmosphere.
Indirect Drying in Various Industries
- Agriculture: Indirect grain dryers ensure no combustion products contact the grain, preserving nutritional properties.
- Whiskey Production: The majority of Scotch whisky distilleries use indirect heating, usually with steam, which allows for a gentler, more controlled heating of the stills.
- Food Processing: Indirect spray drying systems are increasingly used to reduce energy consumption, increase production capacity, and avoid product contamination.
- Chemical Processing: Indirect dryers are preferred for small to medium batches of products that risk contamination or degradation by atmospheric exposure, or that involve toxic or hazardous chemicals.
The Downsides of Direct Fire Drying

While direct fire drying may be faster and less expensive to implement, the disadvantages are considerable:
Health Risks
The formation of carcinogens, exposure to combustion byproducts, and overall poorer air quality render direct fire drying a riskier option.
Environmental Concerns
The release of pollutants into the atmosphere makes direct fire systems less environmentally friendly.
Contamination
Direct contact with combustion products can contaminate the material being dried, affecting the product’s quality.
Uneven Heating
Direct fire methods can lead to uneven heating of the product, making it difficult to control the drying process.
Increased Fire Risk
The direct exposure to flames or hot gases increases the chances of fire, particularly with flammable materials.
Making the Switch: Investing in Health and Quality

While the initial cost of implementing indirect fire drying systems may be higher, the benefits to human health, product quality, and environmental sustainability make it a more sensible investment in the long run. Here are the key benefits:
Healthier Products
Indirect fire drying ensures that food products are free from carcinogenic compounds and other harmful byproducts. This is particularly important for items consumed regularly by humans.
Improved Product Quality
The precise temperature control and gentle heating of indirect drying results in higher-quality products, especially for heat-sensitive materials.
Enhanced Safety
Indirect systems reduce the risk of fire and explosions, creating a safer environment for workers.
Environmentally Friendly
Reduced emissions and better control over combustion byproducts make indirect drying a more sustainable option.
Regulatory Compliance
As regulations become stricter concerning air quality and food safety, indirect fire drying systems are more likely to meet the requirements.
Conclusion
As awareness grows regarding the risks associated with direct fire drying, there is a clear shift toward adopting indirect fire drying technologies. By avoiding direct contact with combustion gases, indirect drying offers a superior alternative, reducing the formation of harmful compounds, enhancing product quality, improving safety, and contributing to a more sustainable future. Although direct fire drying may still be used in some industrial applications, the health and environmental advantages of indirect fire drying are becoming increasingly clear, making it the preferred method for many. The move toward indirect drying represents a step forward in ensuring the products we consume and use are safer and healthier for everyone.