The Objective of This Blog Post
This blog post aims to emphasize the importance of meeting strict regulations such as the Waste Incineration Directive (WID) using Computational Fluid Dynamics (CFD) for incineration engineering. As environmental conservation is a top priority for our customers, ensuring that the waste management process, especially for hazardous waste, meets all the required standards is imperative.
With the aid of CFD simulation, the shortcomings of conventional incineration calculation can be overcome. The integration of emission targets and residence time into the simulation provides a more precise and dependable evaluation of the incineration process.
Utilizing CFD is crucial in meeting strict regulations such as WID for effective waste management. Basic residence-time computations using averages are insufficient to capture the complexities of internal geometry and overall flow rate. In contrast, CFD simulations offer a more accurate assessment of the incineration process. By adhering to WID regulations and employing CFD, we can ensure that we effectively manage waste and significantly reduce the overall environmental impact.
Understanding the Principle of Incineration
Incineration is a process that involves the combustion of organic materials, including solid wastes, non-solid wastes, and foul gas, to produce heat and ash. During this process, by-products such as toxic gases may also be generated. Incineration is considered beneficial for reducing the amount of waste that must be disposed of in landfills and mitigating the risk of groundwater contamination. However, without proper control, it can produce harmful emissions.
Definition of Incineration
Incineration is a crucial process that entails burning organic materials, waste, and foul gas at high temperatures to minimize their volume and mass. This Waste-to-Energy approach reduces waste and produces heat in the form of steam or hot gases. The heat generated can be harnessed to generate electricity or provide heating for buildings and any other useful streams. Incineration is an essential method for managing non-solid waste and mitigating its harmful impact on the environment.
The Process of Incineration
The process of burning waste, called incineration, needs to be done safely and following the Waste Incineration Directive (WID) rules, which apply in European Union countries. To ensure that the waste is completely burned and does not create harmful pollution, the amount of time the waste spends in the incinerator depends on the type of waste being burned. If it is regular household waste, it must be heated for at least 2 seconds at a temperature of 850°C. But if it is hazardous waste, it must be heated for at least 2 seconds at a higher temperature of 1100°C.
After waste is collected and sorted, it undergoes an initial breakdown using a compactor if the particles are too large to enter the incinerator. Then, it is placed into the furnace to be heated up and further broken down into smaller pieces. Any harmful gases that are released are captured and treated before they can be released into the environment. Finally, the remaining ash is collected and disposed of safely.
It is important to note that not all countries use the WID regulations. Instead, other countries like the UK use DEFRA regulations to govern the management of waste. In the USA, the EPA (Environmental Protection Agency) regulates CISWI, while Europe follows EFCA regulations. It is crucial for countries to have regulations in place to ensure that waste management practices are carried out safely and responsibly.
The Benefits and Drawbacks of Incineration
Incineration offers several benefits, including a significant reduction in the amount of waste that must be disposed of in landfills, up to 95% in some cases. This is not only cost-effective but also minimizes the environmental impact of large landfills. Furthermore, incineration can convert solid waste into heat energy and ash, which can help cut down on waste transportation costs. This method can also generate electricity or provide heating for buildings. It is worth noting that incineration can also neutralize the smell of gases produced by waste, making it a crucial solution for reducing unpleasant odours.
However, the drawback of incineration is that it involves burning hydrocarbons, which release a significant amount of CO2 into the atmosphere. As a result, it is essential to have effective emissions control technologies to reduce the environmental impact of incineration.
Limitations of Traditional Incineration and Crude Calculation of Residence Time
Although incineration has many advantages, there are also some limitations to traditional incinerators. One drawback is the potential for producing hazardous emissions if not properly controlled. These emissions can contain pollutants such as dioxins, furans, and heavy metals, which can cause health problems if inhaled or ingested. Additionally, incinerators release substantial amounts of heat, but it is the release of gases like CO2 and CH4 that trigger global warming, rather than the heat itself.
Therefore, proper management of these gases is critical in mitigating the impact of incineration on climate change. Lastly, certain materials burned in incinerators can release toxins that were previously locked away in solid form, which can lead to contamination of surface or groundwater sources if not handled correctly.
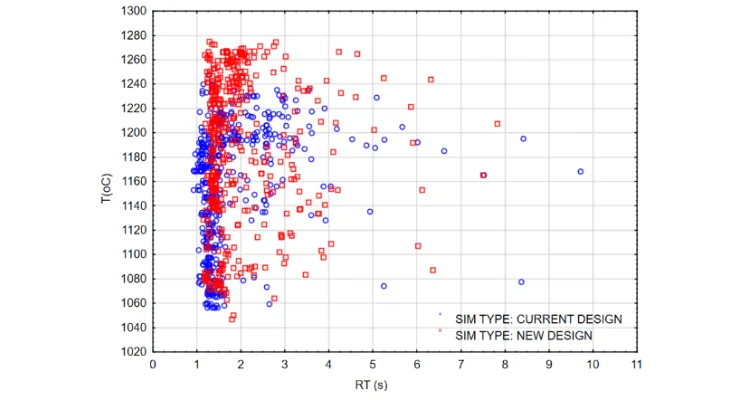
One of the major challenges in traditional incineration is accurately calculating the residence time of the gases in the chamber. Currently, this calculation is done crudely by dividing the chamber volume by the gas flow rate, which only gives an overall average of the residence time. However, this does not consider the different paths and velocities of the gases in the chamber, resulting in an inaccurate estimation of the actual residence time.
What is Computational Fluid Dynamics (CFD)?
Computational Fluid Dynamics (CFD) is a powerful engineering tool used to simulate, analyse, and predict the behaviour of fluids in real-world conditions. This field of study combines numerical algorithms with mathematical models to create detailed computer simulations that accurately represent the physical characteristics of liquids and gases such as temperature, pressure, density, flow velocity, and turbulence. It provides engineers with invaluable insights into the complex dynamics of fluid systems such as combustion chambers, power plants, air conditioning units, and other industrial machinery.
The Power of CFD for Incineration Technology
CFD is a powerful tool used in incineration technology to accurately evaluate the residence time of burning fuel. By computing the path of each particle during its travel, CFD assesses whether its trajectory has had the right amount of time and temperature. A statistical analysis is conducted of all particle tracks, using specific methods such as Monte Carlo simulations or uncertainty quantification, to provide a percentage of particles that meet the required conditions of temperature and velocity.
Ideally, 100% of the particles should meet these conditions. If the percentage falls below 100%, designers can analyse vortex and fast particle paths through the system and work towards reducing them. By using CFD in this way, designers can optimize the performance of incinerators before they are built in real life and ensure compliance with regulations.
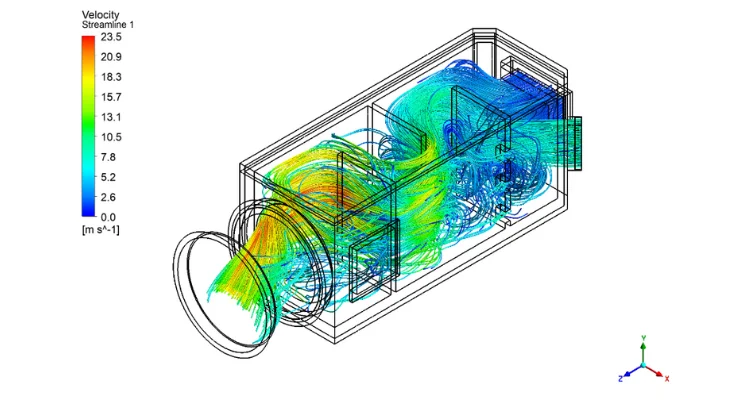
It is important to note that using CFD for incineration technology has some limitations and potential challenges. For example, accurately modelling the complex flow patterns and interactions within the system can be challenging, and the accuracy of the results may depend on the quality of the input data and assumptions made. However, by understanding and accounting for these limitations, CFD can still provide valuable insights and improvements in incinerator design.
CFD Simulations Compared to Traditional Methods
CFD simulations offer significant advantages over traditional methods in optimizing efficiency and reducing emissions in incineration technology. Compared to physical experimentation, CFD requires less time and cost while providing a more comprehensive view of the entire process, including residence time, emissions, velocities, and temperature distributions. CFD results provide greater insight into turbulence and identify potential issues that may not be captured by crude calculations. This accuracy allows for quick adjustments to be made to the system to improve performance and reduce emissions.
Tips for Using CFD
For those who are new to using CFD for incineration technology, here are a few tips to get started:
- For a single-physics simulation, it is necessary to understand the governing equations and boundary conditions that describe the physical phenomena within the system. These include mass, momentum, and energy conservation equations, which can be solved numerically using discretization methods such as finite difference, finite volume, or finite element methods.
- For a multi-physics simulation, in addition to the above equations, other physical phenomena such as chemical reactions, combustion, multi-phase, and radiation heat transfer need to be considered. This requires coupling different physical models to capture the system’s behaviour accurately. For example, a reacting flow simulation may involve coupling a fluid dynamics solver with a combustion chemistry solver.
- The selection of the appropriate modelling approach is critical to obtaining accurate results from a simulation. This involves choosing the appropriate mesh size and resolution to capture the relevant physics in the system. In addition, selecting the right boundary conditions that accurately represent real-world conditions is essential. For example, in a combustion simulation, it is important to accurately specify the inlet air velocity, temperature, and fuel composition.
- After running the simulation, it is crucial to carefully review the results to ensure they are physically meaningful. This includes comparing the results with experimental data or analytical solutions if available. If the results are not accurate, adjustments to the modelling approach may be necessary. These may include modifying the mesh size, changing the boundary conditions, or selecting a different physical model.
Optimizing Incineration Technology with CFD Simulation
Incineration technology involves the use of carefully designed geometries and process design parameters to safely eliminate waste and hazardous materials. The combustion reactions that occur within the incinerator break down the materials into harmless by-products such as water vapour, carbon dioxide, and ash. While reliable in general, there are still many ways to improve efficiency and reduce emissions through advanced optimization techniques such as computational fluid dynamics (CFD).
CFD provides an effective method to simulate the effects of changing burner design, fuel types, and other variables, as well as to evaluate and optimize the geometry and process design parameters of the incinerator. This allows for more precise control over the combustion process, resulting in improved safety, efficiency, and environmental performance.
Efficient Waste Management through Incineration Processes
Waste incineration is a highly efficient and practical approach to managing non-recyclable waste. Incineration processes utilize the heat generated from the combustion of waste to not only reduce the volume of waste but also recover energy that can be utilized for a variety of purposes. Different systems may be employed to achieve the desired outcomes depending on the characteristics of the waste being incinerated. For instance, rotary kilns are commonly employed for high-temperature incineration, owing to their exceptional ability to uniformly distribute heat throughout the incineration chamber.
Designing an Effective Hazardous Waste Incinerator with CFD Simulations
One crucial factor in designing an effective hazardous waste incinerator is ensuring that the waste materials are subjected to adequate residence time and temperature. This is critical to ensure the complete destruction of the contaminants and prevent any residual pollution. By using CFD simulations, we can determine the optimal residence time and temperature conditions required for the incinerator to effectively destroy the hazardous waste. This information can then be used to design an incinerator that meets all regulatory requirements and provides maximum safety and efficiency in the disposal of hazardous materials.
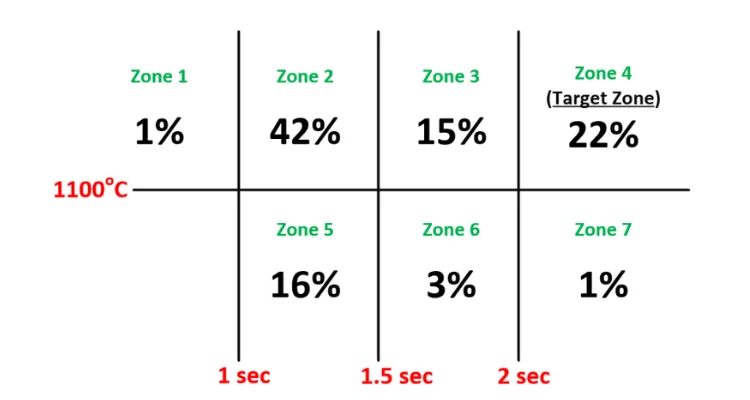
The chart displays the results of CFD analysis (particle tracking) and illustrates the design zones with information on residence time (in seconds) and temperature (in degrees Celsius). Only 22% of the targeted particles meet the necessary requirements. However, when using the standard average calculation from WID, it appears that this design would comply with WID standards.
Conclusion
In conclusion, incineration technology is an important waste management strategy that helps reduce waste volume and produce energy while minimizing the environmental impact of waste disposal. However, to ensure safe and efficient incineration, it is crucial to comply with regulations such as the Waste Incineration Directive (WID) and employ advanced optimization techniques such as Computational Fluid Dynamics (CFD).
By using CFD, designers can accurately evaluate the residence time and optimize the performance of incinerators before they are built in real life or troubleshoot existing problems. This results in improved safety, efficiency, and environmental performance, contributing to the goal of effective waste management and reducing the overall impact on the environment.